Just like before, the build process started with the electronics. So it was time to order new circuit boards and components.
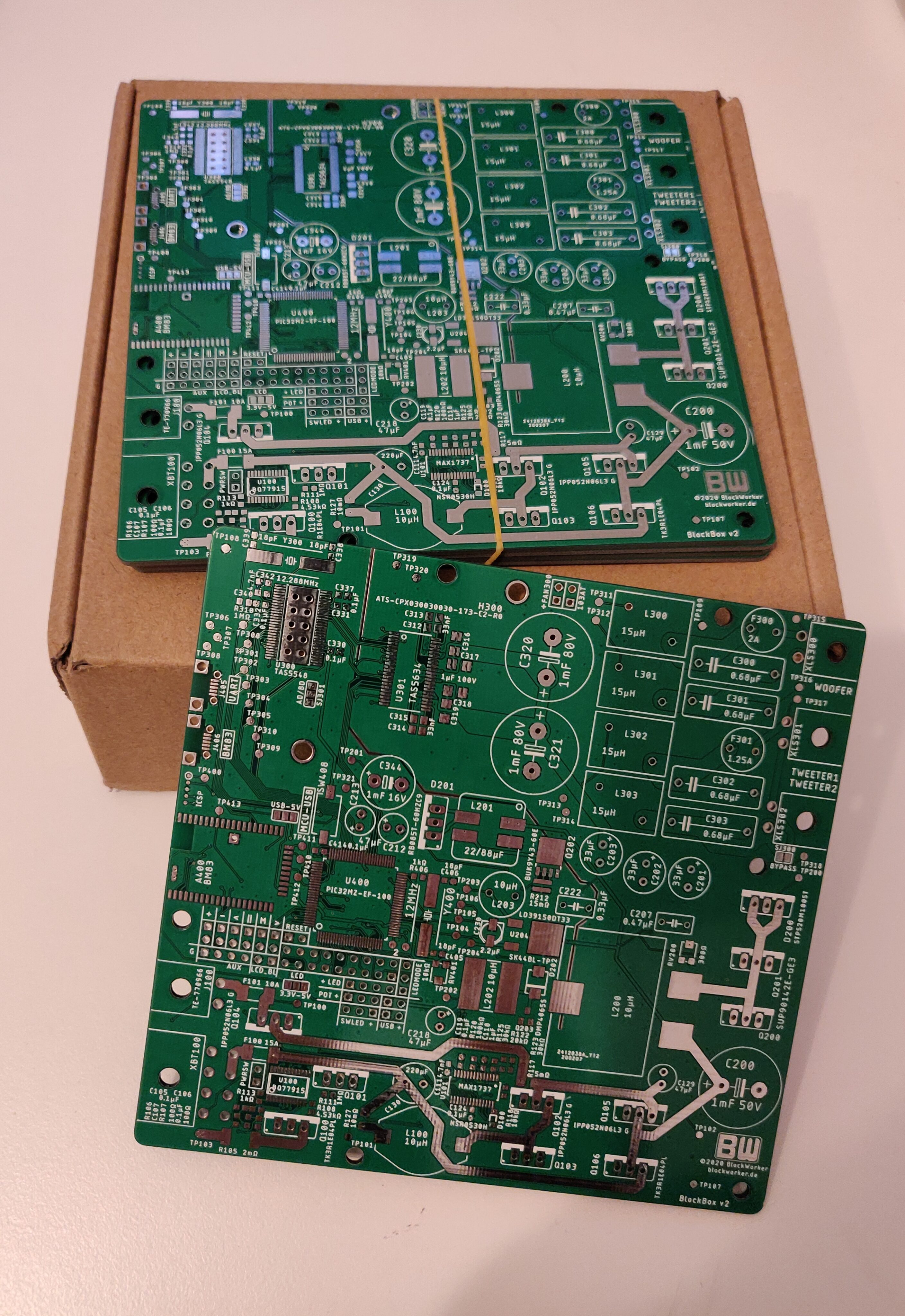
Building the electronics for this second speaker followed the exact same procedure as I described for the BlockBox v1, so I won’t repeat it here. In the end, I had another nice circuit board that looks just slightly different from the first version (shown without the amplifier heat sink here).

Then, it was time for firmware development. This would be a much bigger task than it was for the BlockBox v1, again, because I had to implement a central system controller, as well as touch display communication.
I was able to find a community-made library/driver for the FT81X graphics processor in the display module, which certainly made the job easier, though I had to make quite a few modifications to make it work on the PIC32MZ microcontroller. Aside from that, I implemented my own serial communication drivers for controlling the digital audio processor, Bluetooth module, LEDs, and other peripherals, as well as some central system management logic connecting them together, and of course a user interface for the touchscreen. The firmware source code is available in the same GitHub repository as the electronics design files, though I cannot guarantee anything about its correctness, completeness, and especially code quality (I was quite careless sometimes back then).
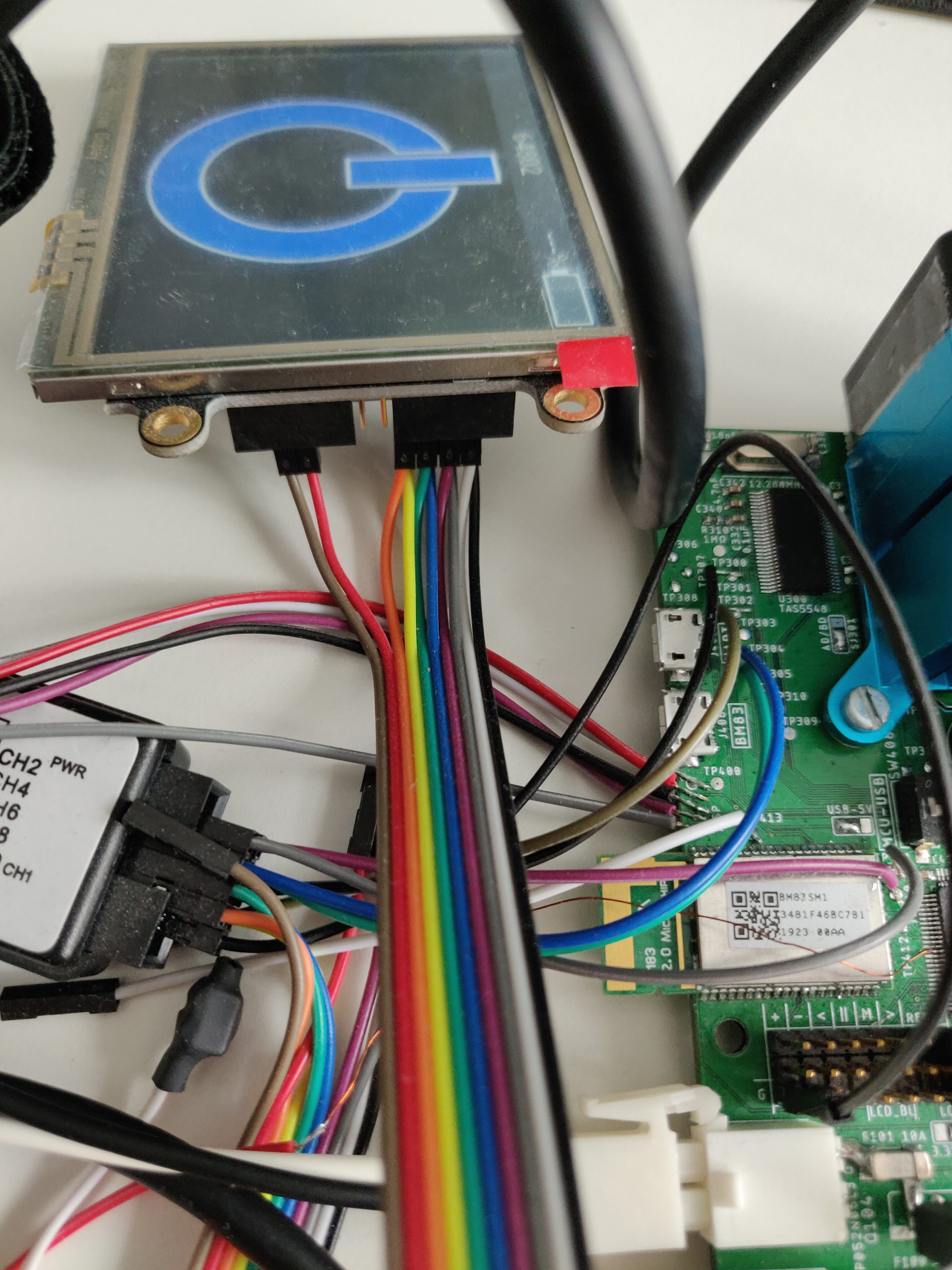
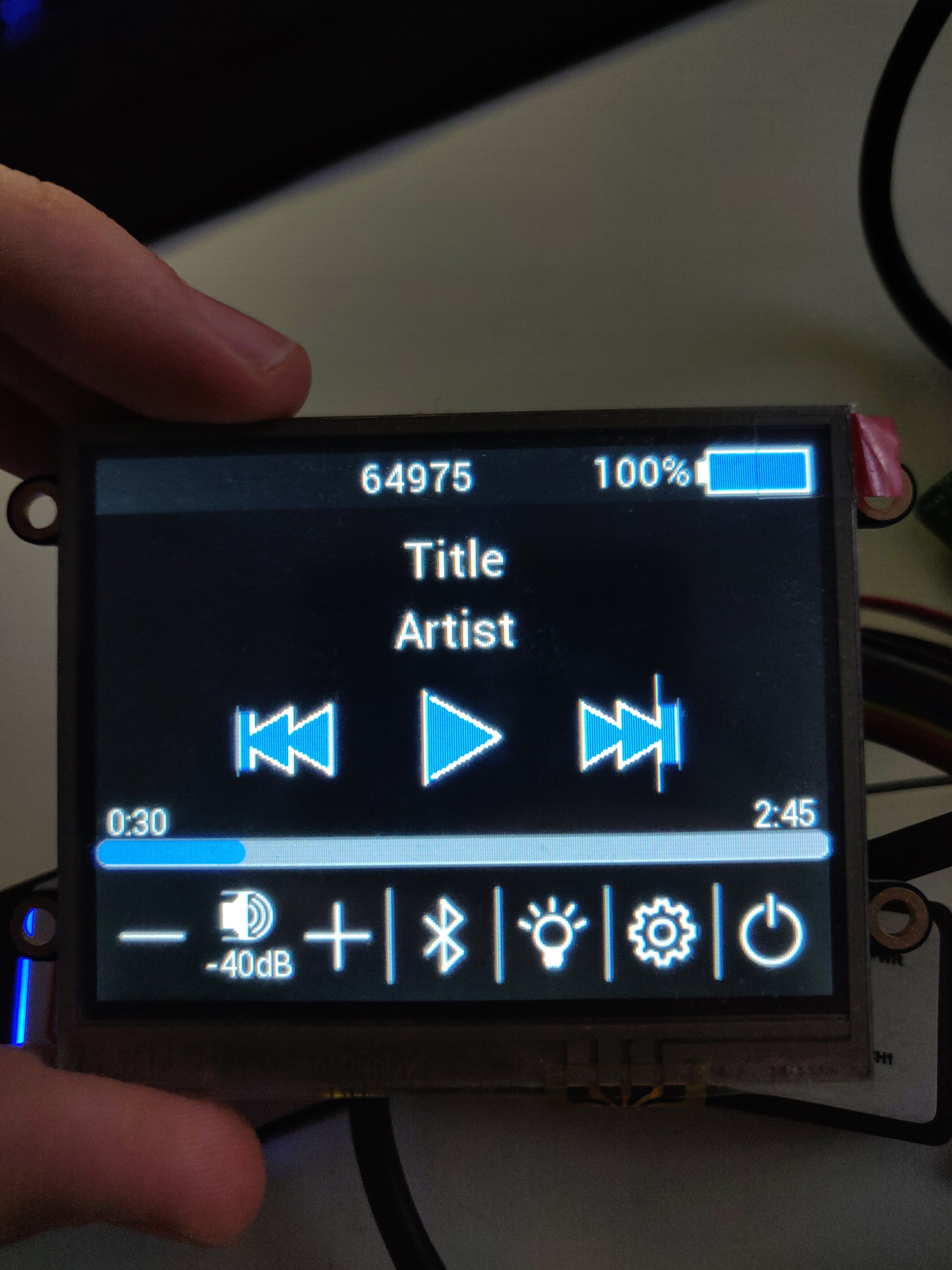
When it came to building the enclosure, however, I knew that my methods from the BlockBox v1 would not be viable any more. Making smaller and simpler shapes using my hand saws may have been possible (even if tedious), but the more complex and much bigger pieces needed for this project would just be too much to ask for. Especially considering the idea I had for LED-lit logos on the sides, which require quite significant precision.
The translucent parts for the LEDs, as well as some black decoration and cover plates, were laser cut out of acrylic plastic, which I was able to order relatively inexpensively.
As for the main enclosure walls, I decided to use CNC milling – thankfully, though a personal connection to a machine shop at my university, I was able to do so for free, as long as I brought the materials and my own CNC programs.
Materials were easy, I just ordered some plain 12mm plywood panels, already cut to the sizes I needed, and got a small piece of aluminium plate stock for the connector panel.
The CNC programs were more complicated – Fusion 360 has some great tools for CNC programming based on my CAD design, but as I’d never done anything like that before, it took me a while to research, understand, and learn the basics of machining and CNC programming.
In the end, it was time for some machining.
With that, I had some rough-looking side panels, which would need quite a bit of post-processing to remove extra tabs and pieces, sand down sharp/rough edges, file away unwanted internal corner radii, and so on.
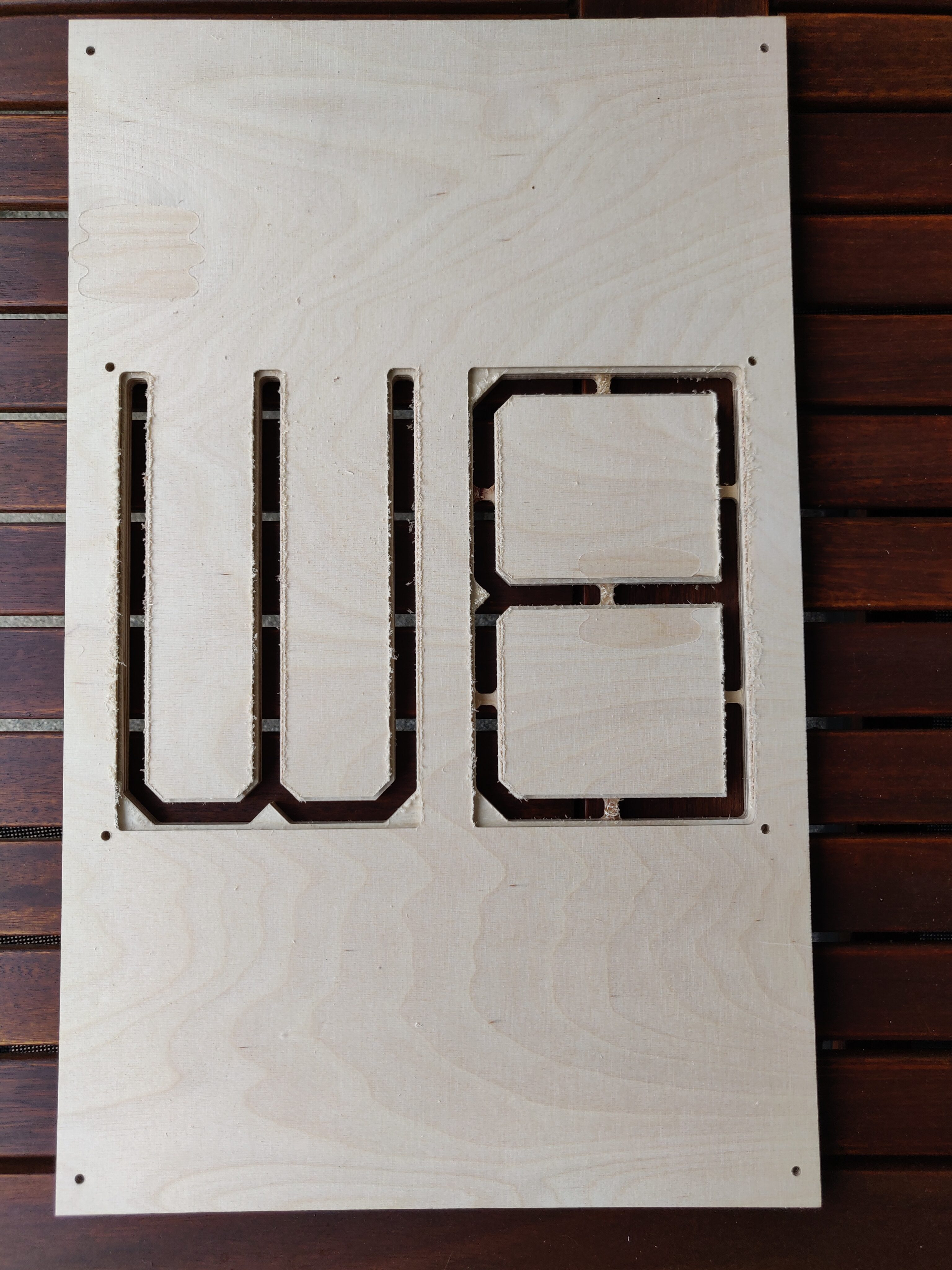
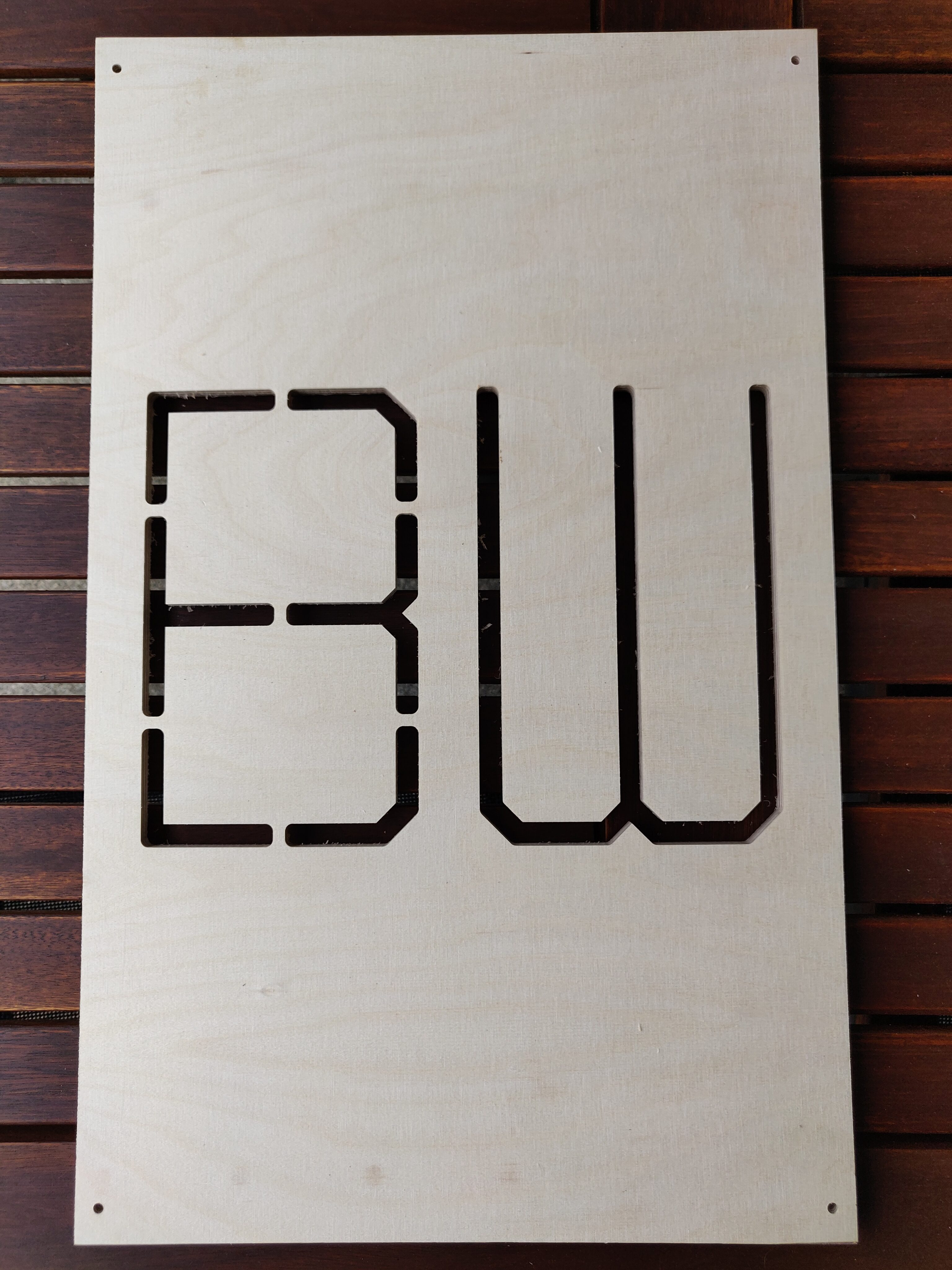
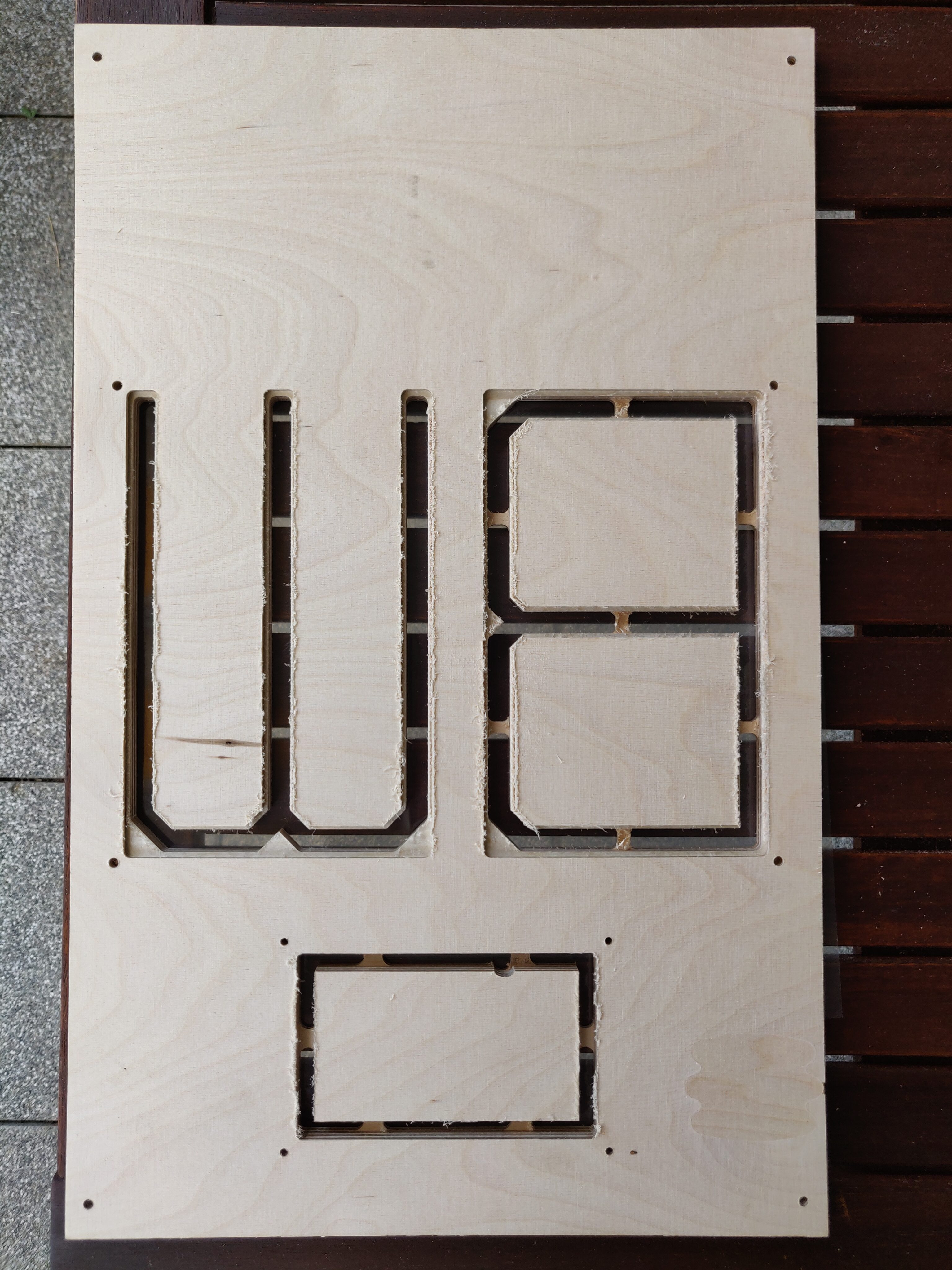
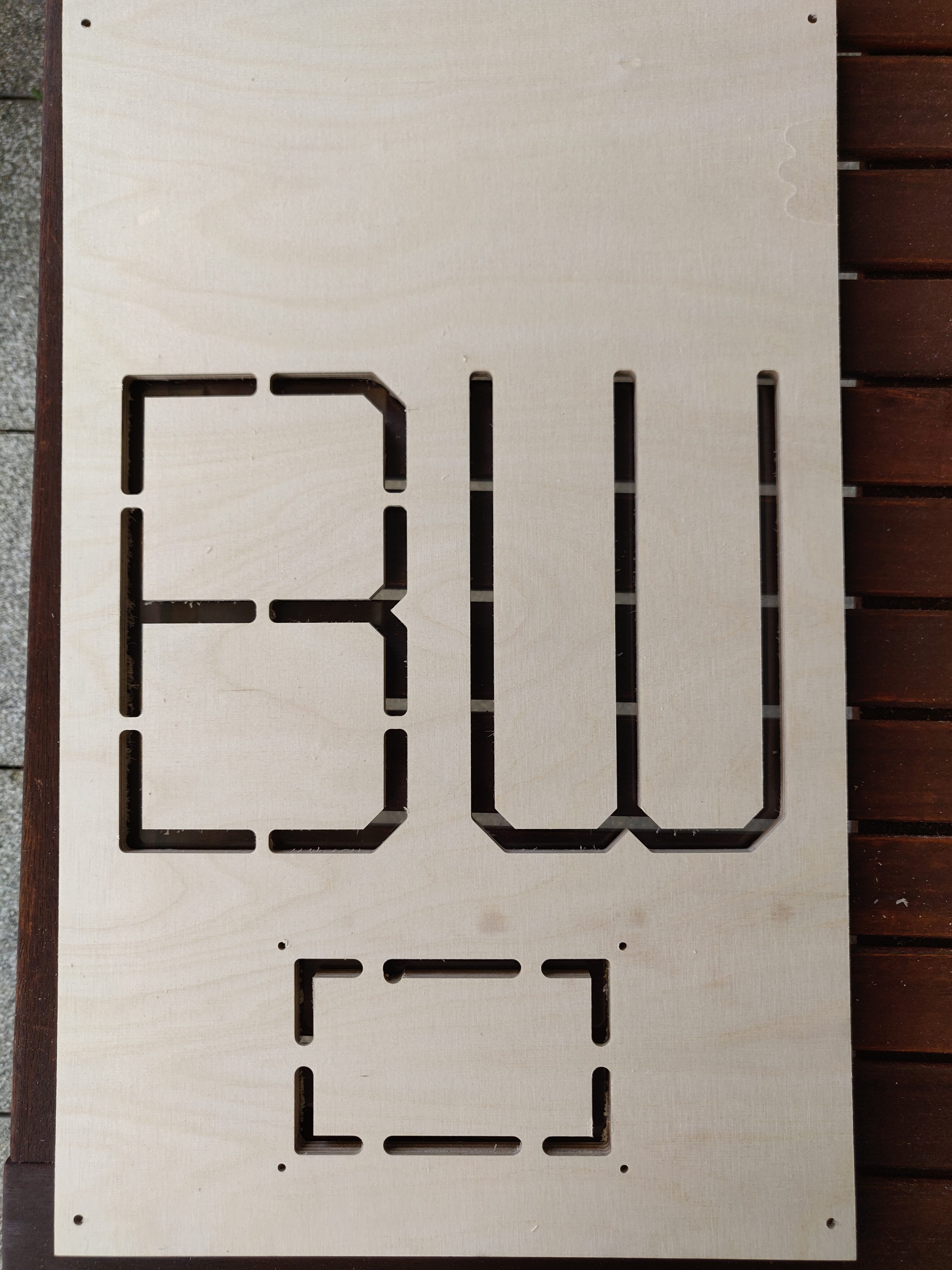
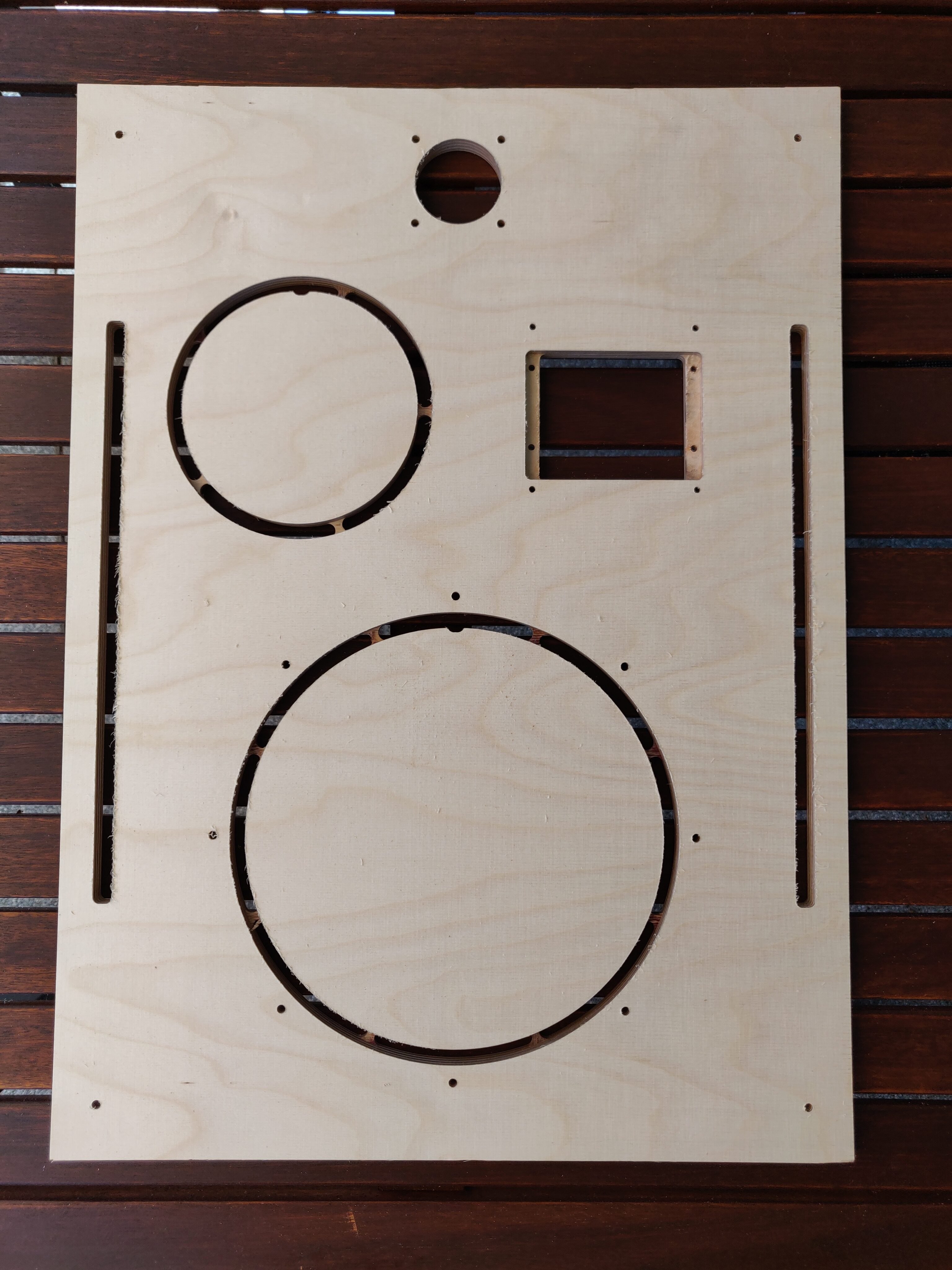
After post-processing, they looked much better, and also fit the acrylic pieces nicely.

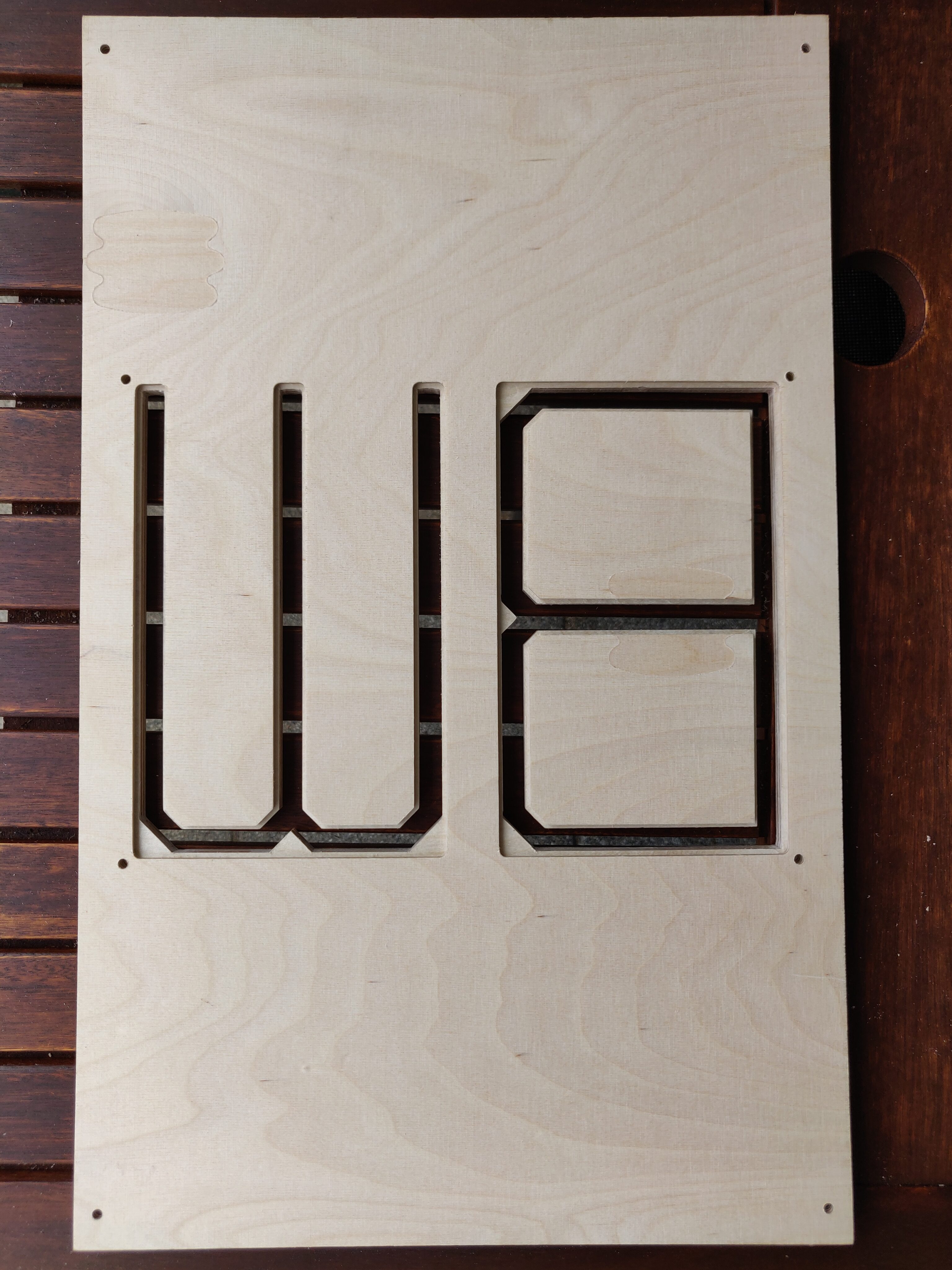
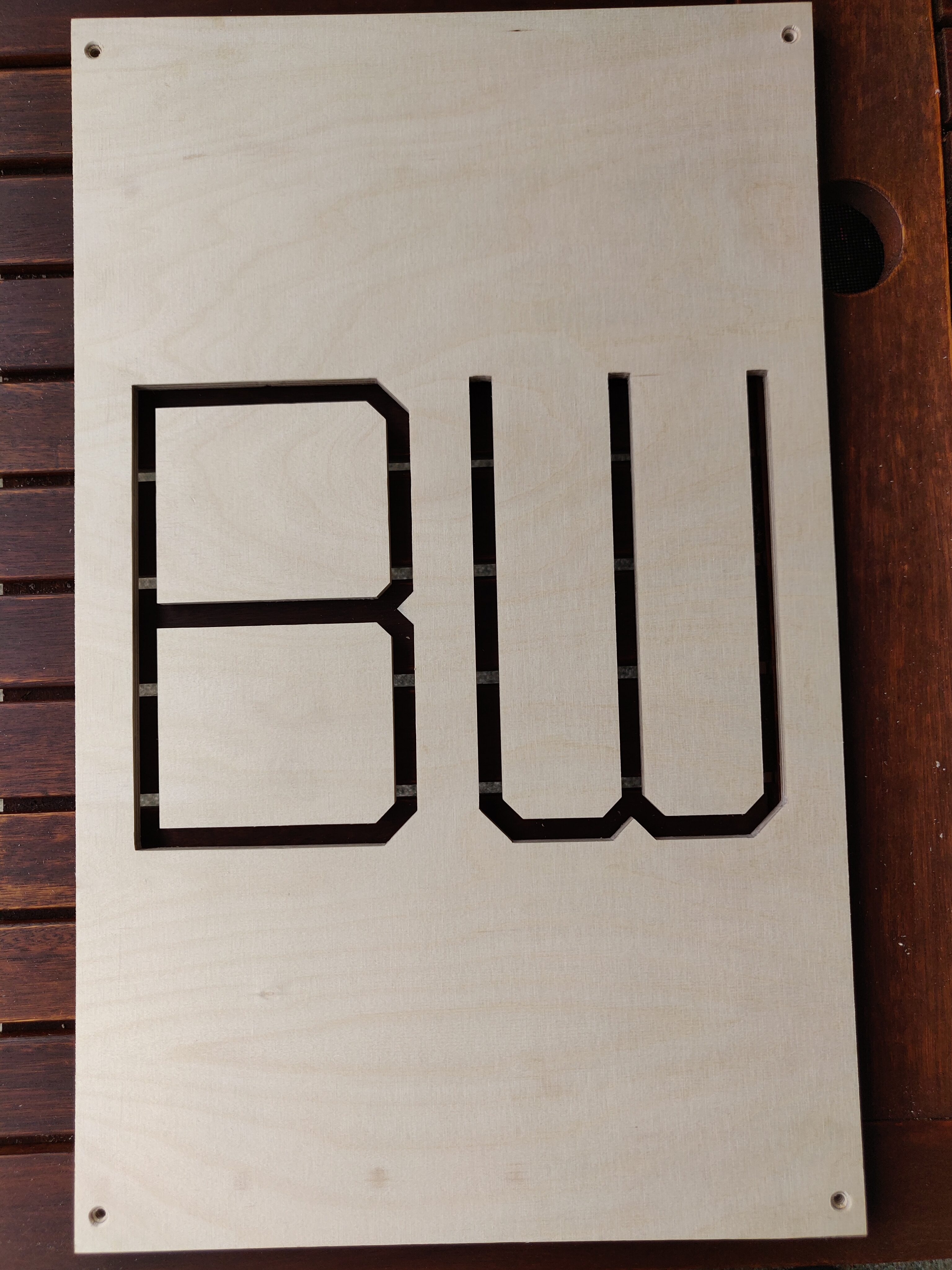
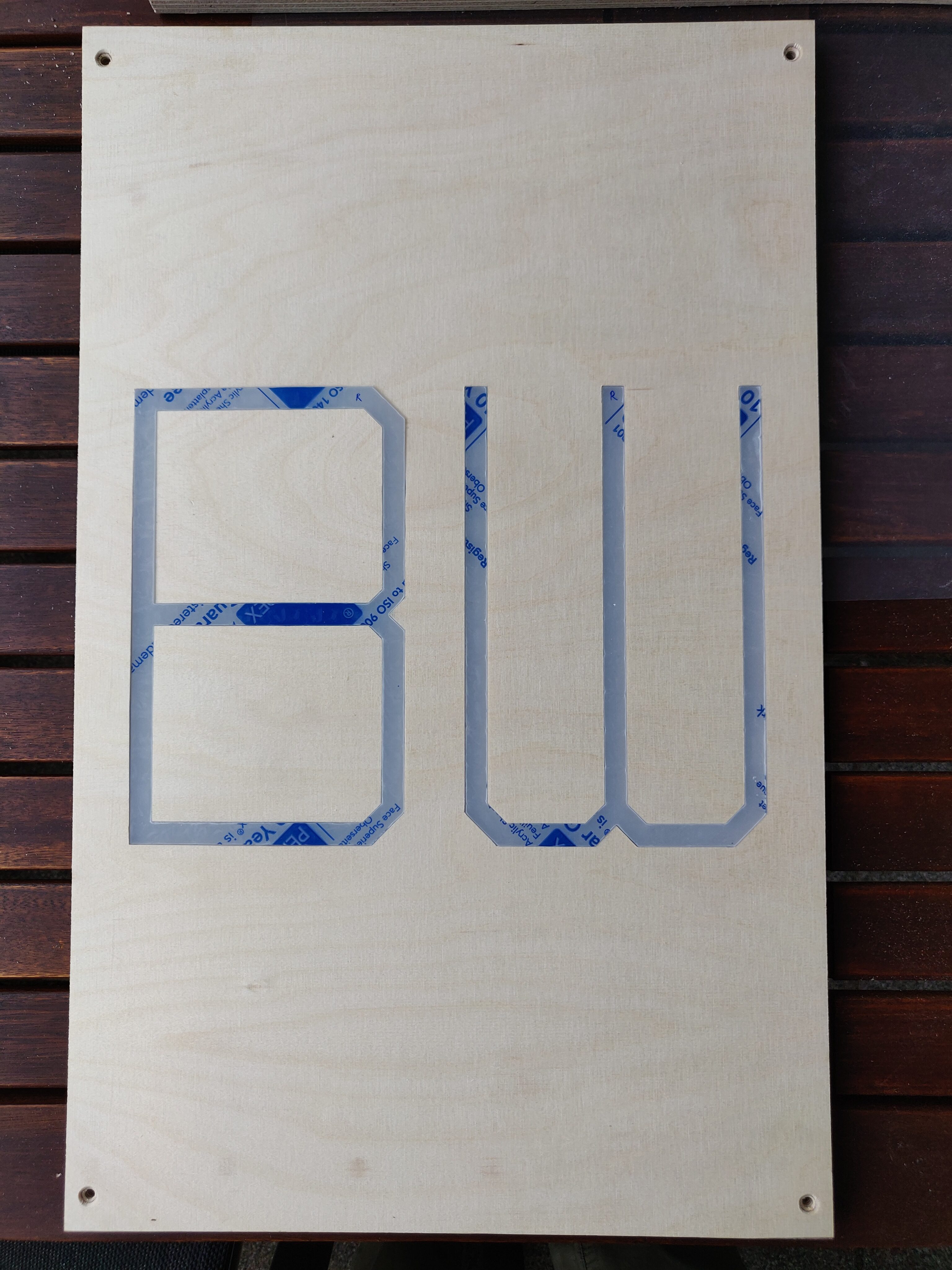
Now it was time to assemble the speaker. I built the main wooden box by screwing the walls together using metal corner pieces, then hand-cut some extra plates with LED strips to go behind the acrylic inserts, installed the drivers, port resonator, display, circuit board, connector plate, battery, and some plastic wool for acoustic damping inside the enclosure.

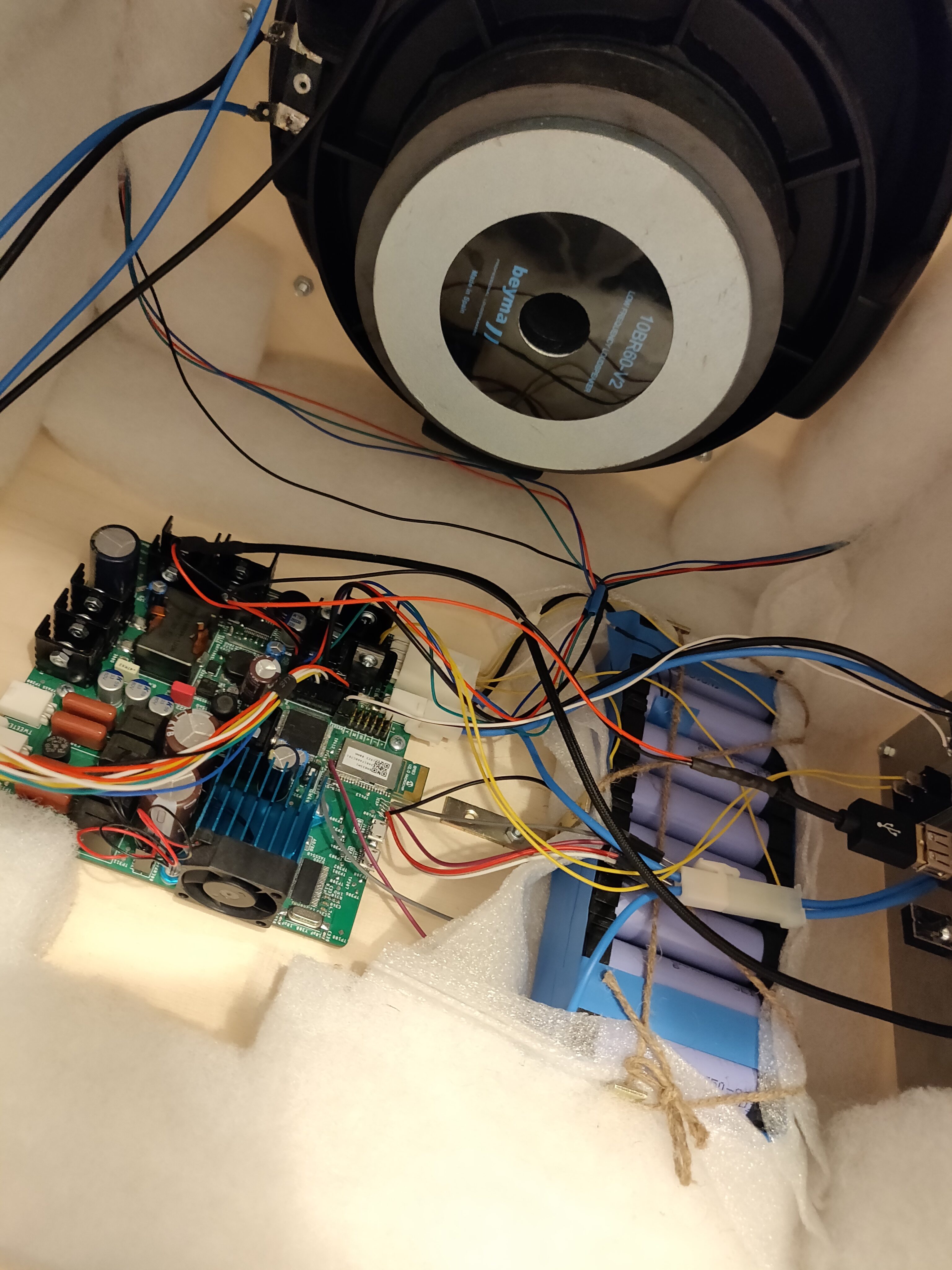
With everything connected and closed up, the BlockBox v2 was complete.
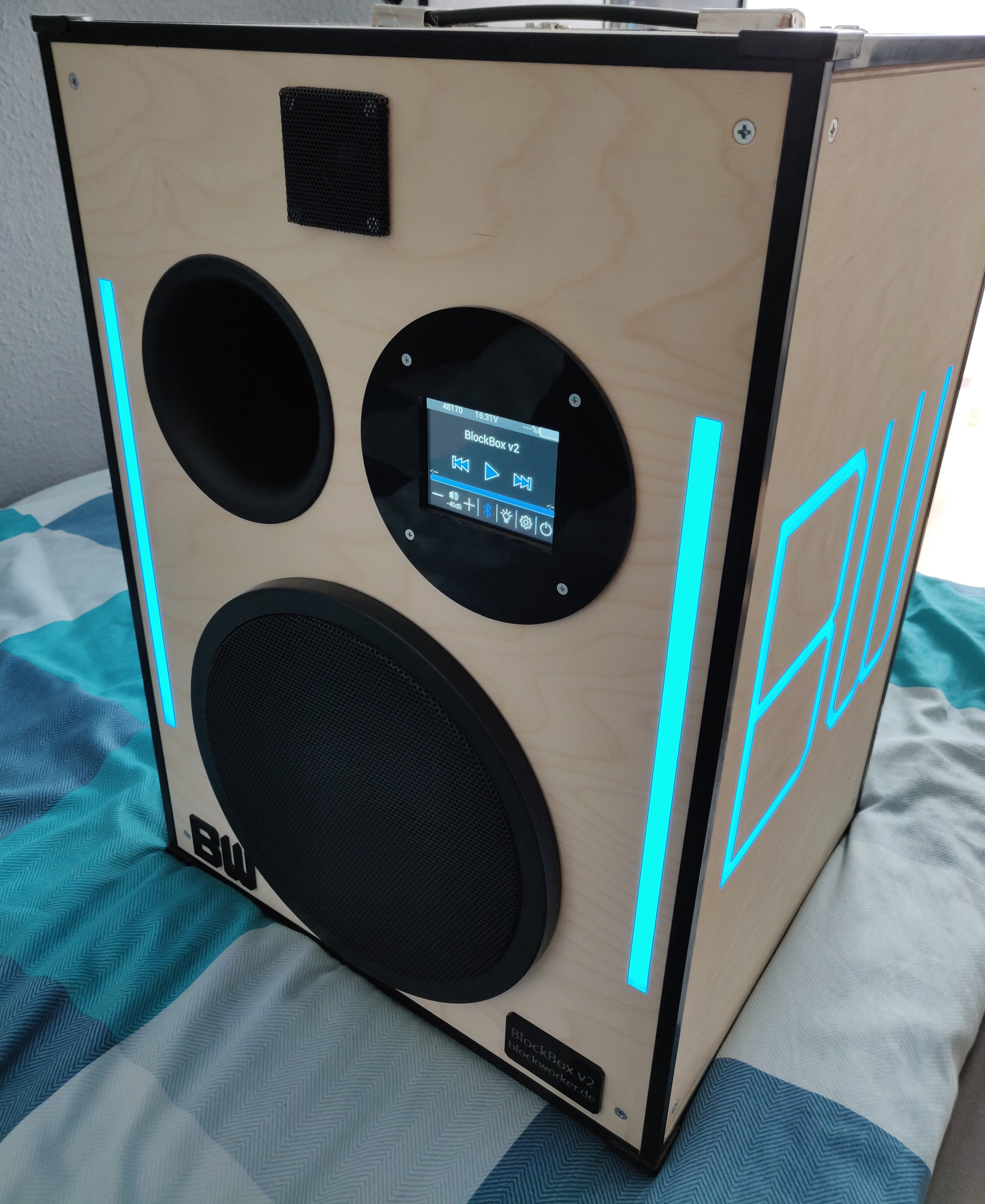
However, since my circuit had a nice digital audio processor that I could control, I decided to improve the sound a little more, using some EQ optimisation.
Leave a Reply