After the completion of the BlockBox v1, I really thought for a while that I’d be done with this idea. And it only took a few months for me to prove myself wrong, with the BlockBox v2 project.
But this time it felt different – I really was done, at least for now. The BlockBox v2 has its flaws, there are certainly ways to improve it further, but overall… I’m just really happy with it, and very proud of the results of my work – especially if I look at both speakers next to each other.
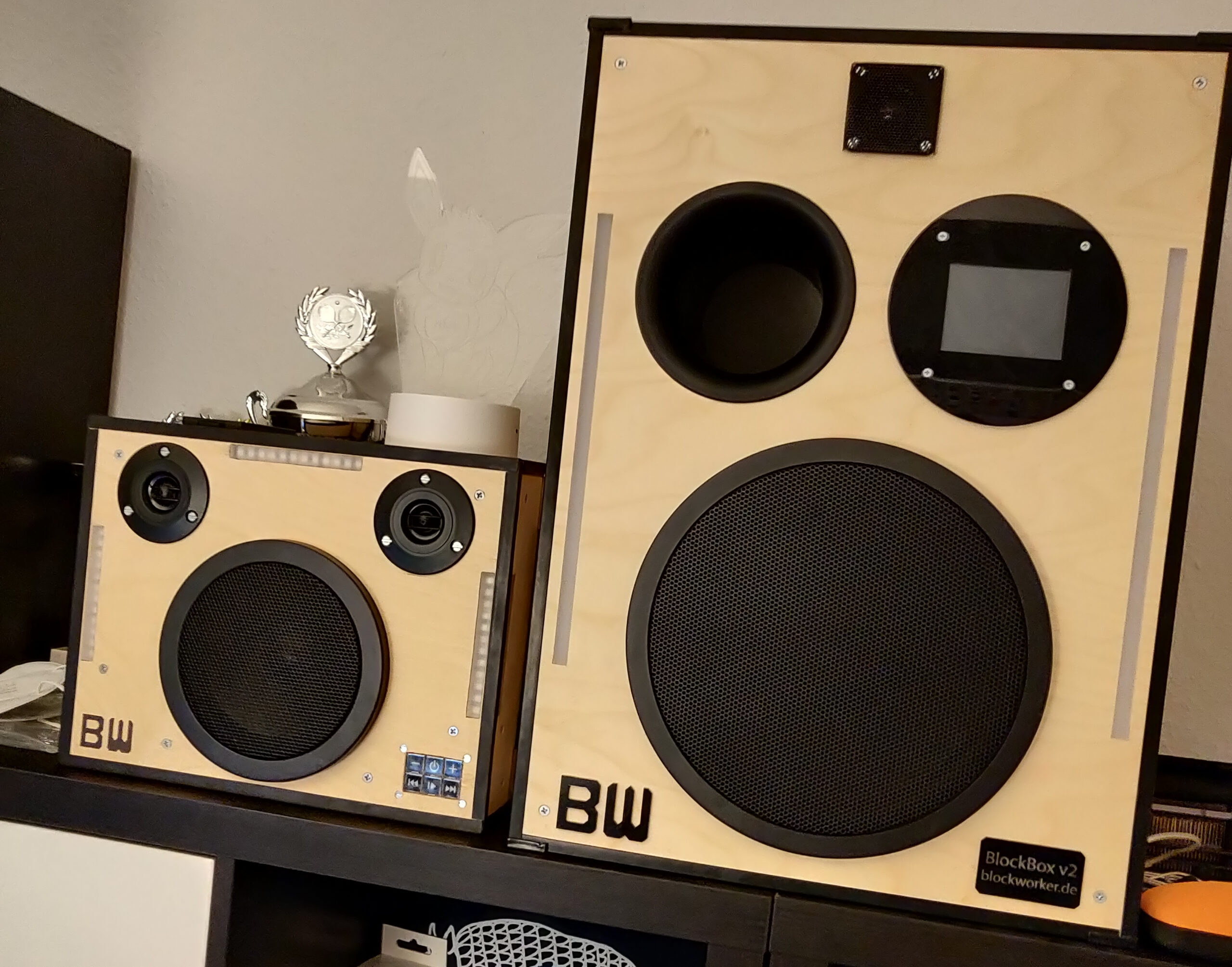
Let’s look at the features of the final product:
- Two-way cross-over speaker system with digital audio path
- 100W 10″ low-frequency driver
- 50W hi-fi tweeter
- -3dB bass roll-off frequency around 38Hz
- Theoretical maximum sound pressure level around 110-113dB (@ 1m)
- Bluetooth audio playback (SBC or AAC), effective range ~10-15m
- Touchscreen interface with lots of audio settings and playback control
- EQ-optimised sound profile (to the best of my abilities)
- (Roughly) music-synchronised LEDs
- 166Wh battery (in practice, lasts for more than 10 hours of continuous playback)
- Battery protection and fast charging
- 2x External USB (5V 1.5A) for phone charging
- Optional analog AUX input (not implemented due to lack of practical need)
Looking back at this huge project of building two speakers, I can only say one thing: It was absolutely worth it.
Now, are the speakers by themselves worth it? No, not really. Because I had to buy everything in single-piece quantities, restrict myself quite heavily in terms of what I could work with using the tools I had, and over-engineered many things “just to be safe”, they ended up being wayyyy too expensive to compete with commercially available speakers, at around 1500€ (for both combined) – and that’s if I ignore the cost of the months of work that went into them.
But the main value of this project, for me, was not in the speakers themselves, but the incredible amount of learning and experience that I gained throughout this project, including audio engineering, mechanical design, CAD and manufacturing, electronics design and soldering of course, and microcontroller firmware development.
This is where my speaker-building journey would end for now, but I had a feeling I would be back to it sooner rather than later, in another project.